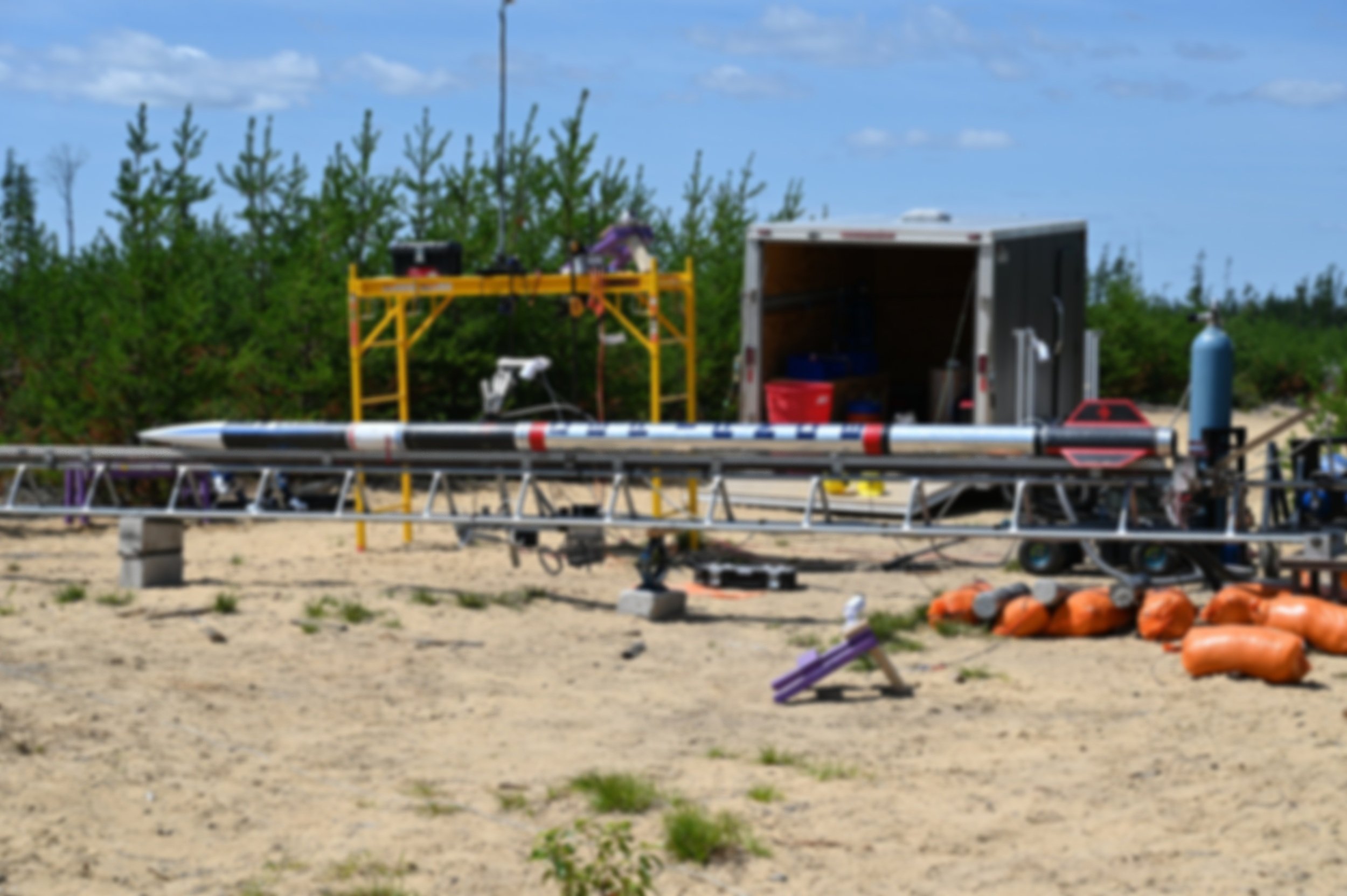
Rocketry
The UTAT Rocketry division has a mission to develop expertise in the design of high-altitude sounding rockets. We accomplish this in three fields of rocketry by developing hybrid, liquid, and solid engined rockets at a variety of scales.
Project Overview
Defiance
Achievements and Records
With the Defiance series, UTAT Rocketry holds a series of records:
First experimental hybrid launch in Canada - flown in August 2022. Achieved an apogee 21,000 ft at the inaugural Launch Canada competition
Highest altitude Student Research and Developed (SRAD) advanced engine in Canada. Achieved an apogee of 30,500 ft and top speed of Mach 1.4 at Launch Canada 2024
And has earned podium places at Launch Canada, three years in a row:
First Place in the Advanced Category - LC2022
Third Place in the Advanced Category - LC2023
Second Place in the Advanced Category - LC2024
Defiance is a hybrid-propellant rocket that UTAT has been developing since 2017, with a target altitude of 30,000 ft. Defiance uses parachute recovery and has several telemetry modules which relay GPS coordinates from the nose cone and avionics bay of the rocket to the ground station operators. The entire project and the necessary infrastructure to operate it (such as cold flow and hot fire engine test stands) have been developed, built, and tested by UTAT Rocketry.
Originally, Defiance was designed for an altitude of 60,000 ft, aiming to break the Canadian amateur rocketry altitude record with a hybrid. We later decided through various testing results that the aspect ratio of such a slender rocket would not be structurally viable, and we decided to reduce the rocket's length and consequently the altitude target.
In the end, we broke a different kind of record, achieving the first experimental hybrid rocket flown in Canada.
This is an incredible achievement for the University of Toronto. It took a monumental effort from everyone involved and the invaluable effort of the University of Toronto Institute of Aerospace Studies, UTIAS, who provided us with the facilities and space needed to test and build Defiance. It was truly a project that redefined limits!
Vehicle Architecture
Rocket Name: Defiance
Vehicle Configuration: Single Stage
Propulsion System: N₂O / Paraffin Hybrid Engine
Propellant Load: 16.9 kg N₂O Oxidizer / 3.8 kg Paraffin Wax Fuel Core
Total Impulse: 38,428 Ns
Airframe Length: 546 cm / 215 in
Airframe Diameter: 14 cm / 5.5 in
Dry Mass: 39.61 kg / 87.32 lbs
Wet Mass: 61.89 kg / 136.4 lbs
Nosecone
6-ply fibreglass construction
The nosecone is connected to the recovery system by a bulkhead and eye nut at its shoulder. The bulkhead can be removed to access the payload volume.
Recovery Bay
10-ply carbon fibre construction
Section of the airframe housing all of the recovery hardware. The recovery system is connected to the vehicle by an eye nut at the bottom of the bay.
Avionics Bay
15-ply 3 mm fibreglass tubes construction
Section of the airframe housing the two COTS flight computers, radio, GPS and power supply.
Fill Bay
10-ply carbon fibre construction
Section of the airframe housing the engine fill system. The bay houses the plumbing and actuators used to load the oxidizer tank with propellant. It also contains a N2 bottle used to pressurise the tank.
Oxidizer Tank
Al 6061-T6 construction with a wall thickness of 3.175 mm
The oxidizer tank holds the N₂O oxidizer at 800 psig during and before the burn. It is loaded through the Fill Bay which is connected to the fill system on the ground.
Combustion Chamber
Al 6061-T6 construction with a wall thickness of 3.175 mm
The combustion chamber contains the paraffin wax fuel core. Oxidizer is fed through a shower head injector at the top.
Fin Can / Boat Tail
Fin Can: 4-ply carbon fibre construction
Houses a graphite nozzle for the engine. The fins provide a stability margin of 4.1 cal.
Discovery
Discovery is the team’s first-ever liquid propellant rocket. This project aims to grow our expertise in liquid engine development, with the ultimate goal of developing a liquid rocket that can breach the Karman line, reaching the edge of space. Discovery has a target altitude of 10,000 ft and will serve as a stepping stone toward future high-altitude liquid projects.
Solid Rocket Certification Program
One of our key initiatives is a solid rocket certification program, which trains our members with basic rocketry and prepares them for engaging more thoroughly with the team.
Team Structure
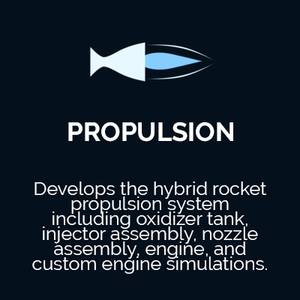
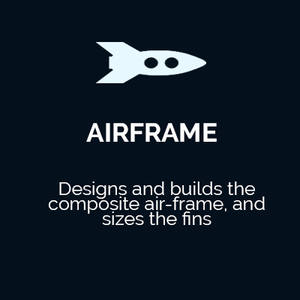
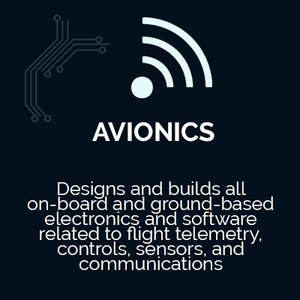
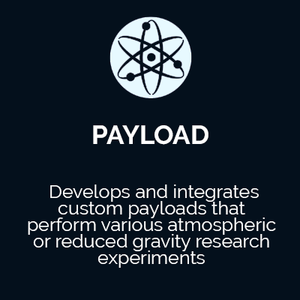
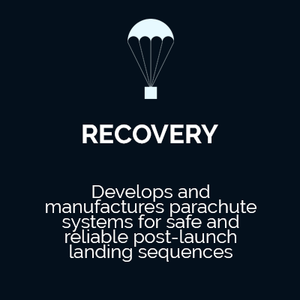
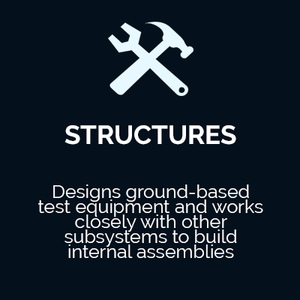
Team Leadership
-
Joséa Tarulli
Director of Rocketry
-
Liam Xue
Liquid Chief Engineer
-
Bhakti Chohan
Hybrid Chief Engineer
-
Rodrigo Salazar
Hybrid Project Manager
-
Timo Lahteenmaa-Swerdlyk
Solid Project Manager
-
Lianne Choong
Operations Manager
-
Will Taylor
Liquid Systems Project Manager
Rocketry Leads
-
Nat Espinosa
Aerodynamics Lead
-
Nadim Hatoum
Aerodynamics Lead
-
Jocelyn Wall
Airframe Lead
-
Jack A Amodeo
Airframe Lead
-
Abdul Asa'd
Hybrid Propulsion Lead
-
George Chen
Hybrid Propulsion Lead
-
Kaida Xu
Recovery Lead
-
Akhil Ambardekar
Liquid Propulsion Lead
-
Yubo Wang
Liquid Propulsion Lead
-
Julia Xu
Structures Lead
-
Joao Pedro Boaventura
Structures Lead
-
Aspen Erlandsson
Avionics Leads
-
Jessie Lin
Avionics Lead
-
Jaival Patel
Software Lead
Portfolio Leads
-
Mashoodah Patel
Business Development Specialist
-
Kira Modylevsky
Logistics Specialist
-
Sabiha Ahmad
Brand & Media Specialist
-
Kota Yamakawa
Finance Specialist
-
Eryn Richardson-Bartha
Outreach Liaison
-
Talon De Freitas
Chief Safety Officer
-
Oliver Harrison
Secondary Safety Officer